What’s New in Multifamily: Building Processes
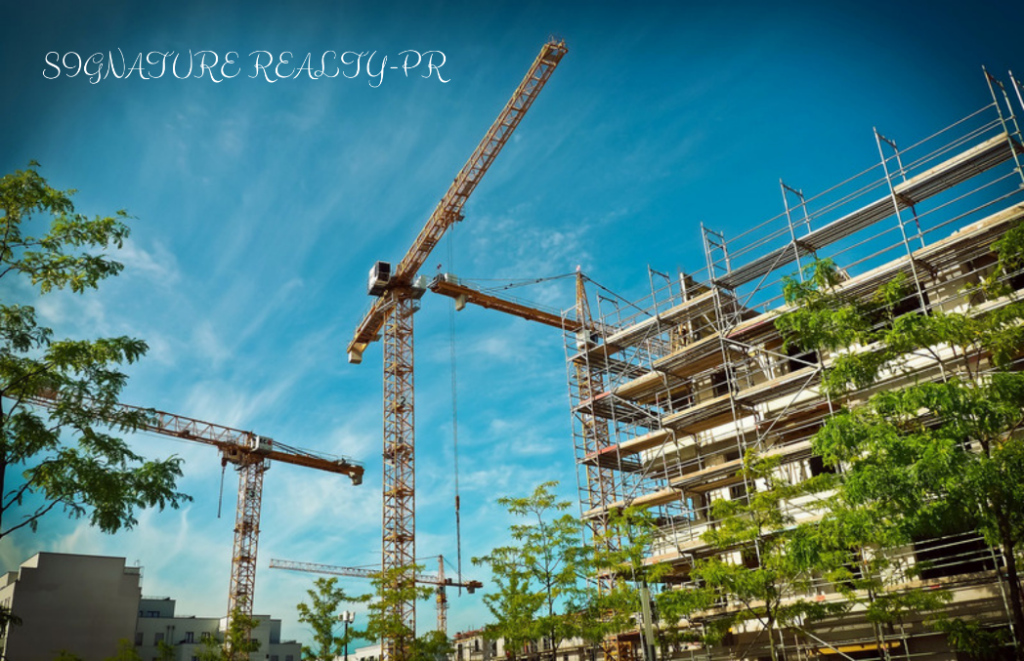
On the multifamily front, high costs and a greater concern for the environment are spurring efforts to cut construction time and expense while in, Three Key Takeaways
- Mass timber products save construction time because of its prefabrication.
- The materials sequester carbon rather than emit it as concrete and steel do.
- Wood exposed on the interior provides a biophilic effect, a boon to aesthetics and healthfulness.
In the multifamily space, the need for new building processes and materials and the possibility of paring construction and labor costs are generating a buzz. This is especially true as rising costs and inflation, labor shortages and an increased concern for the environment continue to impact the industry.
Among a few, one solution, mass timber, stands out as a viable option that could help alleviate builder woes. The “large pre-manufactured, multilayered, solid wood panels” check many of the boxes for developers, according to the American Wood Council. They’re fire resistant, strong, sustainable and reduce construction and labor costs.
Though it took a while to gain traction in the United States, the use of mass timber is on the rise, which means more real estate clients might make the choice to live in a building with this construction.
The Emergence of Prefabricated Wood
Wood has long been used to construct multifamily residential and commercial buildings, but in the 1800s and 1900s, concrete and steel replaced it in many cases. The reason? So buildings could rise higher. European architects and builders focused again on wood as a smart, renewable environmental choice that could take carbon from the air and sequester it versus concrete and steel that emit it, says architect Zac Miles, AIA, with architecture firm KTGY.
In factories overseas, Europeans were first to engineer mass timber pieces into large wood panels for floors and walls, and they attached them through cross-laminated timber layers (CLT), nail laminated timber (NLT), or dowel laminated timber (DLT), says Dan Getz, structures global practice director at global design firm HKS architects. These prefabricated panels provide strength comparable to concrete and steel floor systems and got the code approval go-ahead for use in buildings taller than those constructed from non-engineered wood members, Getz says.
Volatility in lumber and resin prices due to the pandemic, bad weather where plants were located, and other challenges caused some issues in 2021. “Supply chain disruptions caused a step backward,” says Christian Beard, director of building products research at John Burns Real Estate Consulting. Once prices stabilized, however, interest was reignited, he says.
Already 1,571 residential and commercial multifamily mass timber buildings have been constructed, according to Woodworks, a nonprofit that tracks these numbers and provides education and other support related to U.S. wood buildings, says Bill Parsons, chief operating officer. Almost 200 are under development with the majority in the seven to 12-story range and designed for multifamily housing. While there were once few factories in North America, the domestic numbers are increasing, says architect Susan Jones, FAIA founding architect of atelierjones LLC. Among her current projects is the eight-story Heartwood building in Seattle for the nonprofit Community Roots Housing. Jones and others point out that tall wood, mass timber buildings will appeal more to others as their benefits are recognized:
Shorter Timetables and Lower Costs
Because these buildings are comprised of prefabricated members, construction time is less, and labor costs are lower. Korb estimates the installation time for Ascent was cut by one quarter versus other construction. The project also required a crew of 11 versus a typical team of 40 for a comparable concrete building. The shorter time cycle also means that these buildings generally get to market and into the revenue stream faster, says architect Rockland Berg, AIA, NCARB, principal and director of business development at the Dallas-based architecture firm, three. This appeals to developers watching timelines because of higher interest rates, says Vaughan Buckley, CEO of Volumetric Building Companies, a vertically integrated volumetric modular construction technology company. To boot, work at sites to lift panels is also quieter, Jones says.